DAQ1500 User Guide: Difference between revisions
No edit summary |
No edit summary |
||
Line 1: | Line 1: | ||
__NOINDEX__ | __NOINDEX__ | ||
__NOTOC__ | |||
<metadesc>The Wheatstone Bridge Phidget measures up to 2 load cells or Wheatstone Bridge-based sensors and connects to a VINT port.</metadesc> | <metadesc>The Wheatstone Bridge Phidget measures up to 2 load cells or Wheatstone Bridge-based sensors and connects to a VINT port.</metadesc> | ||
[[Category:UserGuide]] | [[Category:UserGuide]] | ||
== | ==Part 1: Setup== | ||
{{UGIntro|DAQ1500}} | {{UGIntro|DAQ1500}} | ||
*[{{SERVER}}/products.php?product_id=DAQ1500 DAQ1500 - Wheatstone Bridge Phidget] | *[{{SERVER}}/products.php?product_id=DAQ1500 DAQ1500 - Wheatstone Bridge Phidget] | ||
Line 19: | Line 20: | ||
<br clear="all"> | <br clear="all"> | ||
{{UGIntroDone|DAQ1500}} | {{UGIntroDone|DAQ1500}} | ||
{{UGcontrolpanel|DAQ1500}} | {{UGcontrolpanel|DAQ1500}} | ||
== Part 2: Using Your Phidget == | |||
===About=== | |||
The DAQ1500 reads two load cells, strain gauges or Wheatstone Bridge-based sensors. The Phidget reports results as a voltage ratio. To convert from voltage ratio to a quantity like weight or force, see the Calibration Guide in the Advanced Topics section. | |||
== | ===Explore Your Phidget Channels Using the Control Panel=== | ||
== | |||
You can use your Control Panel to explore your Phidget's channels. | |||
'''1.''' Open your Control Panel, and you will find the following channels: | |||
[[Image:DAQ1500_Panel.jpg|link=|center]] | |||
'''2.''' Double click on a channel to open an example program. Each channel belongs to the '''Voltage Ratio Input''' channel class: | |||
{{UGC-Start}} | |||
{{UGC-Entry|Voltage Ratio Input (Bridge Input):|Read data from a load cell | |||
| | |||
In your Control Panel, double click on "Bridge Input": | |||
[[Image:DAQ1500-VoltageRatio.jpg|800px|center|link=]]}} | |||
{{UGC-End}} | |||
{{UG-Part3}} | |||
== Part 4: Advanced Topics and Troubleshooting == | |||
{{UGC-Start}} | |||
The | {{UGC-Entry|Choosing a Gain Value| | ||
[[Image:DAQ1500- | | | ||
The DAQ1500 has the option to change the bridge gain, which improves measurement resolution at the cost of reducing your effective range. We recommend starting at 128x gain and testing your load cell with the maximum load you expect to see in your system. If you get any saturation error events, you should lower the gain and test again. Here are the specifications that vary with gain: | |||
[[Image:DAQ1500-gain.jpg|center|850px|link=]] | |||
}} | |||
{{UGC-Entry|Connecting Your Strain Gauge or Load Cell| | |||
| | |||
Load cells are pressure sensors that can be used with the DAQ1500. For more information, see our [[Load Cell Primer]]. | |||
If no documentation is available for your strain gauge, it is possible to use a multimeter to determine how to connect it, provided there are no electronics in the sensor. Measure resistance between the 4 wires. There are 6 wire combinations - two of the wire combinations will have a resistance 20-40% higher than the other four. Select one of the two high-resistance combinations, and wire it into 5V and G on the DAQ1500. Connect the other two wires into +/-. Apply a load, if the V/V responds in the opposite way to your expectations, flip the +/- wires.}} | |||
{{UGC-Entry|Measurement Considerations| | |||
| | |||
The DAQ1500 is designed to measure voltages as a ratio of the supply voltage - it is not practical to make measurements of absolute voltages with this product. | |||
For maximum accuracy, all wires from the DAQ1500 to the sensor should be the same length, thickness, and temperature (as the temperature will change the resistance of the wires). | |||
The bridge inputs can be powered down, reducing power consumption with DAQ1500 sensors. Powering down the bridge inputs is also useful for preventing the heating of sensors, which can introduce errors. Due to the drift that occurs during self-heating, we recommend you operate your DAQ1500 in one of two ways: | |||
{{ | * Allow a 30-minute warm-up after the channel is enabled, before taking constant measurements for an extended period. The drift, due to self-heating of the wires, will eventually stop. Once stable, you can calibrate and measure. | ||
* For occasional measurements, you should enable the channel, immediately take the measurement, and then disable the channel. By doing this, there is so little current moving through the wires that the device does not get a chance to heat up. You can also follow this process when calibrating.}} | |||
{{UGC-Entry|The number I’m getting back from the DAQ1500 is really small| | |||
| | |||
Load cells output a small voltage proportional to the amount of strain they are currently experiencing. The rated output for most load cells at full load is in the order of millivolts, so when you’re only straining the load cell at a fraction of its full load, you will get very small values. In order to convert to meaningful units like grams or newtons, you need to [[Calibrating_Analog_Sensors|calibrate]] the load cell.}} | |||
{{UGC-Entry|Calibration| | |||
| | |||
For an in-depth guide on calibration, see [[Calibrating Analog Sensors]].}} | |||
{{UGC-DataInterval}} | |||
{{UGC-Addressing}} | |||
{{UGC-End}} |
Revision as of 18:20, 21 April 2020
Part 1: Setup
Welcome to the DAQ1500 user guide! In order to get started, make sure you have the following hardware on hand:
- DAQ1500 - Wheatstone Bridge Phidget
- VINT Hub
- Phidget cable
- USB cable and computer
- something to use with the DAQ1500 (e.g. load cell, strain gauge, etc.)
Next, you will need to connect the pieces:
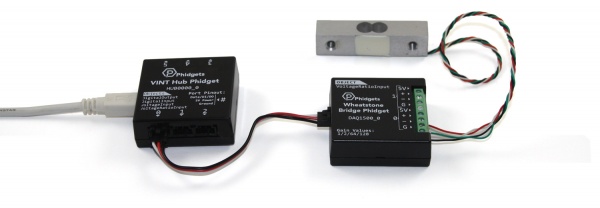
- Connect the DAQ1500 to the VINT Hub using the Phidget cable.
- Connect a load cell or strain gauge to the DAQ1500. See your product's data sheet for connection details.
- Connect the VINT Hub to your computer with a USB cable.
Now that you have everything together, let's start using the DAQ1500!
Phidget Control Panel
In order to demonstrate the functionality of the DAQ1500, the Phidget Control Panel running on a Windows machine will be used.
The Phidget Control Panel is available for use on both macOS and Windows machines.
Windows
To open the Phidget Control Panel on Windows, find the icon in the taskbar. If it is not there, open up the start menu and search for Phidget Control Panel
macOS
To open the Phidget Control Panel on macOS, open Finder and navigate to the Phidget Control Panel in the Applications list. Double click on the icon to bring up the Phidget Control Panel.
For more information, take a look at the getting started guide for your operating system:
Linux users can follow the getting started with Linux guide and continue reading here for more information about the DAQ1500.
First Look
After plugging the DAQ1500 into your computer and opening the Phidget Control Panel, you will see something like this:
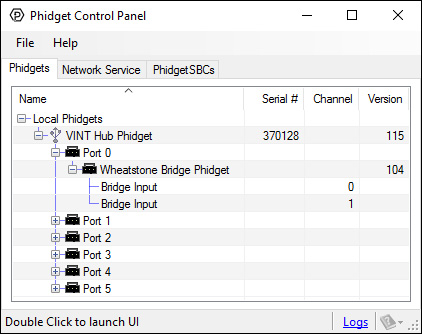
The Phidget Control Panel will list all connected Phidgets and associated objects, as well as the following information:
- Serial number: allows you to differentiate between similar Phidgets.
- Channel: allows you to differentiate between similar objects on a Phidget.
- Version number: corresponds to the firmware version your Phidget is running. If your Phidget is listed in red, your firmware is out of date. Update the firmware by double-clicking the entry.
The Phidget Control Panel can also be used to test your device. Double-clicking on an object will open an example.
Part 2: Using Your Phidget
About
The DAQ1500 reads two load cells, strain gauges or Wheatstone Bridge-based sensors. The Phidget reports results as a voltage ratio. To convert from voltage ratio to a quantity like weight or force, see the Calibration Guide in the Advanced Topics section.
Explore Your Phidget Channels Using the Control Panel
You can use your Control Panel to explore your Phidget's channels.
1. Open your Control Panel, and you will find the following channels:
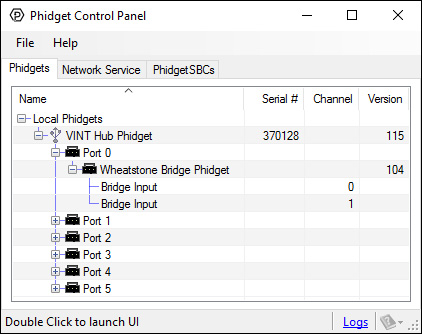
2. Double click on a channel to open an example program. Each channel belongs to the Voltage Ratio Input channel class:
In your Control Panel, double click on "Bridge Input":
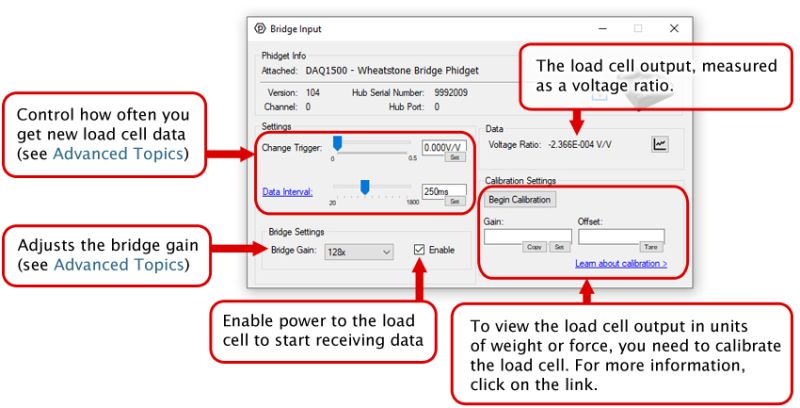
Part 3: Create your Program
Part 4: Advanced Topics and Troubleshooting
The DAQ1500 has the option to change the bridge gain, which improves measurement resolution at the cost of reducing your effective range. We recommend starting at 128x gain and testing your load cell with the maximum load you expect to see in your system. If you get any saturation error events, you should lower the gain and test again. Here are the specifications that vary with gain:
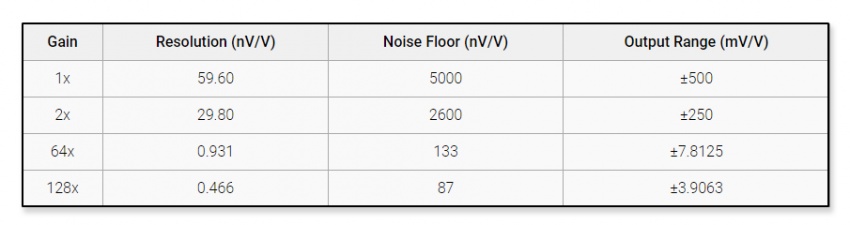
Load cells are pressure sensors that can be used with the DAQ1500. For more information, see our Load Cell Primer. If no documentation is available for your strain gauge, it is possible to use a multimeter to determine how to connect it, provided there are no electronics in the sensor. Measure resistance between the 4 wires. There are 6 wire combinations - two of the wire combinations will have a resistance 20-40% higher than the other four. Select one of the two high-resistance combinations, and wire it into 5V and G on the DAQ1500. Connect the other two wires into +/-. Apply a load, if the V/V responds in the opposite way to your expectations, flip the +/- wires.
The DAQ1500 is designed to measure voltages as a ratio of the supply voltage - it is not practical to make measurements of absolute voltages with this product. For maximum accuracy, all wires from the DAQ1500 to the sensor should be the same length, thickness, and temperature (as the temperature will change the resistance of the wires). The bridge inputs can be powered down, reducing power consumption with DAQ1500 sensors. Powering down the bridge inputs is also useful for preventing the heating of sensors, which can introduce errors. Due to the drift that occurs during self-heating, we recommend you operate your DAQ1500 in one of two ways:
- Allow a 30-minute warm-up after the channel is enabled, before taking constant measurements for an extended period. The drift, due to self-heating of the wires, will eventually stop. Once stable, you can calibrate and measure.
- For occasional measurements, you should enable the channel, immediately take the measurement, and then disable the channel. By doing this, there is so little current moving through the wires that the device does not get a chance to heat up. You can also follow this process when calibrating.
Load cells output a small voltage proportional to the amount of strain they are currently experiencing. The rated output for most load cells at full load is in the order of millivolts, so when you’re only straining the load cell at a fraction of its full load, you will get very small values. In order to convert to meaningful units like grams or newtons, you need to calibrate the load cell.
For an in-depth guide on calibration, see Calibrating Analog Sensors.
The Change Trigger is the minimum change in the sensor data needed to trigger a new data event.
The Data Interval is the time (in ms) between data events sent out from your Phidget.
The Data Rate is the reciprocal of Data Interval (measured in Hz), and setting it will set the reciprocal value for Data Interval and vice-versa.
You can modify one or both of these values to achieve different data outputs. You can learn more about these properties here.
Before you open a Phidget channel in your program, you can set these properties to specify which channel to open. You can find this information through the Control Panel.
1. Open the Control Panel and double-click on the red map pin icon:
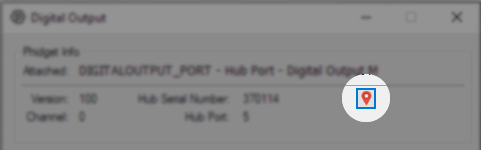
2. The Addressing Information window will open. Here you will find all the information you need to address your Phidget in your program.
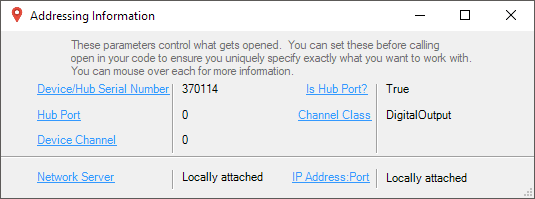
See the Phidget22 API for your language to determine exact syntax for each property.