1046 User Guide: Difference between revisions
No edit summary |
No edit summary |
||
Line 9: | Line 9: | ||
</div> | </div> | ||
==Using | == Part 2: Using Your Phidget == | ||
===About=== | |||
The PhidgetBridge reads up to four load cells, strain gauges or Wheatstone Bridge-based sensors. The Phidget reports results as a voltage ratio. To convert from voltage ratio to a quantity like weight or force, see the '''Calibration Guide''' in the Advanced Topics section. | |||
===Explore Your Phidget Channels Using the Control Panel=== | |||
You can use your Control Panel to explore your Phidget's channels. | |||
'''1.''' Open your Control Panel, and you will find the following channels: | |||
[[Image:1046_Panel.jpg|link=|center]] | |||
'''2.''' Double click on a channel to open an example program. Each channel belongs to the '''Voltage Ratio Input''' channel class: | |||
{{UGC-Start}} | |||
{{UGC-Entry|Voltage Ratio Input (Bridge Input):| Read data from a load cell | |||
| | |||
In your Control Panel, double click on "Bridge Input": | |||
[[Image:1046-VoltageRatio.jpg|800px|center|link=]]}} | |||
{{UGC-End}} | |||
{{UG-Part3}} | |||
== Part 4: Advanced Topics and Troubleshooting == | |||
{{UGC-Start}} | |||
{{UGC-Graphing}} | |||
{{UGC-Entry|Choosing a Gain Value| | |||
| | |||
We report the measured voltage in a ratiometric unit known as V/V. This is how the maximum range of sensors that use strain gauges is usually specified. V/V is the output value in V of the measured sensor, scaled for a 1V sensor supply voltage. This value will correspond to the physical quantity that the sensor is measuring, regardless of the actual voltage supplied to the sensor. | We report the measured voltage in a ratiometric unit known as V/V. This is how the maximum range of sensors that use strain gauges is usually specified. V/V is the output value in V of the measured sensor, scaled for a 1V sensor supply voltage. This value will correspond to the physical quantity that the sensor is measuring, regardless of the actual voltage supplied to the sensor. | ||
Line 70: | Line 78: | ||
Some wheatstone bridges, most often those produced from silicon and used in pressure sensors, will have a very wide offset, and large manufacturing variation in the offset. This will restrict the gain to lower settings, particularly if the application must support a number of deployed systems with the expected variation. Fortunately, the very high precision electronics used in the 1046 means that in many application, higher gain is not necessary to get adequate accuracy and resolution. | Some wheatstone bridges, most often those produced from silicon and used in pressure sensors, will have a very wide offset, and large manufacturing variation in the offset. This will restrict the gain to lower settings, particularly if the application must support a number of deployed systems with the expected variation. Fortunately, the very high precision electronics used in the 1046 means that in many application, higher gain is not necessary to get adequate accuracy and resolution. | ||
}} | |||
{{UGC-Entry|Connecting Your Strain Gauge or Load Cell| | |||
| | |||
Load cells are pressure sensors that can be used with the 1046. For more information, see our [[Load Cell Primer]]. | Load cells are pressure sensors that can be used with the 1046. For more information, see our [[Load Cell Primer]]. | ||
Line 77: | Line 86: | ||
If no documentation is available for your strain gauge, it’s possible to use a multimeter to determine how to connect it, provided there are no electronics in the sensor. First, measure resistance between the 4 wires. There are 6 combinations - two combinations will have a resistance 20-40% higher than the other four. Choose one of these high-resistance combinations, and wire it into 5V and G on the 1046. Connect the other two wires into +/-. Apply a load, if the V/V responds in the opposite way to your expectations, flip the +/- wires. | If no documentation is available for your strain gauge, it’s possible to use a multimeter to determine how to connect it, provided there are no electronics in the sensor. First, measure resistance between the 4 wires. There are 6 combinations - two combinations will have a resistance 20-40% higher than the other four. Choose one of these high-resistance combinations, and wire it into 5V and G on the 1046. Connect the other two wires into +/-. Apply a load, if the V/V responds in the opposite way to your expectations, flip the +/- wires. | ||
{{UGC-Entry|Measurement Considerations| | |||
| | |||
The 1046 is designed to measure voltages as a ratio of the supply voltage - it’s not practical to make measurements of absolute voltages with this product. | The 1046 is designed to measure voltages as a ratio of the supply voltage - it’s not practical to make measurements of absolute voltages with this product. | ||
Line 84: | Line 94: | ||
Each bridge input can be powered down, reducing power consumption with 1046 sensors, and useful for reducing heating of sensors, which can introduce errors. | Each bridge input can be powered down, reducing power consumption with 1046 sensors, and useful for reducing heating of sensors, which can introduce errors. }} | ||
{{UGC-Entry|The number I’m getting back from the 1046 is really small| | |||
| | |||
Load cells output a small voltage proportional to the amount of strain they are currently experiencing. The rated output for most load cells at full load is in the order of millivolts, so when you’re only straining the load cell at a fraction of its full load, you will get very small values. In order to convert to meaningful units like grams or newtons, you need to [[Calibrating_Analog_Sensors|calibrate]] the load cell.}} | |||
{{UGC-Entry|Calibration| | |||
| | |||
We have observed a 1.5% difference between a 1x gain and an 8x gain. This may require that each system (1046 and sensors) be calibrated as a whole. For maximum accuracy, decide on, and keep with a chosen gain before calibrating the system. | |||
Expensive sensors will ship with a certificate of calibration specifying, often in mv/V, how the sensor responds to stimulus. Less expensive will have to be calibrated | |||
For an in-depth guide on calibration, see [[Calibrating Analog Sensors]].}} | |||
{{UGC-Entry|Measuring RTDs| | |||
| | |||
{{RTDinfo}} | {{RTDinfo}} | ||
}} | |||
{{ | {{UGC-DataInterval}} | ||
{{UGC-Addressing}} | |||
{{UGC-End}} |
Revision as of 19:30, 16 March 2021
Part 1: Setup
Part 2: Using Your Phidget
About
The PhidgetBridge reads up to four load cells, strain gauges or Wheatstone Bridge-based sensors. The Phidget reports results as a voltage ratio. To convert from voltage ratio to a quantity like weight or force, see the Calibration Guide in the Advanced Topics section.
Explore Your Phidget Channels Using the Control Panel
You can use your Control Panel to explore your Phidget's channels.
1. Open your Control Panel, and you will find the following channels:
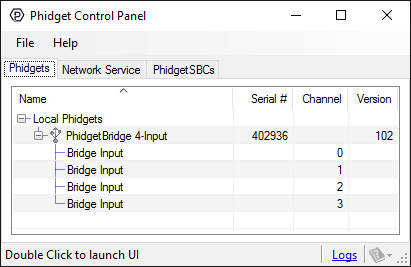
2. Double click on a channel to open an example program. Each channel belongs to the Voltage Ratio Input channel class:
In your Control Panel, double click on "Bridge Input":
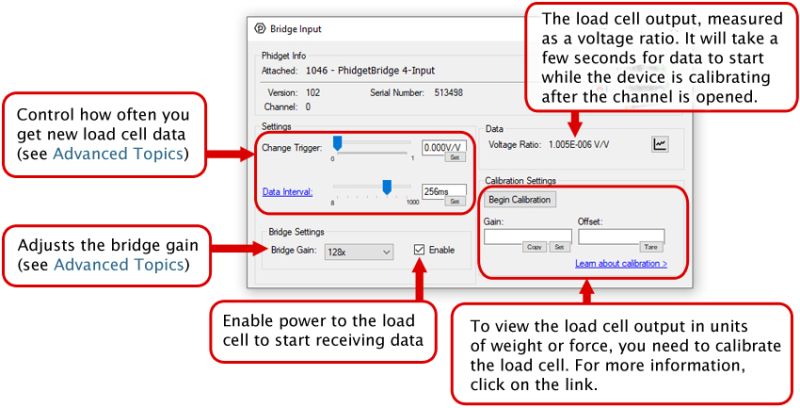
Part 3: Create your Program
Part 4: Advanced Topics and Troubleshooting
Note: Graphing and logging is currently only supported in the Windows version of the Phidget Control Panel.
In the Phidget Control Panel, open the channel for your device and click on the icon next to the data type that you want to plot. This will open up a new window:
If you need more complex functionality such as logging multiple sensors to the same sheet or performing calculations on the data, you'll need to write your own program. Generally this will involve addressing the correct channel, opening it, and then creating an Event Handler and adding graphing/logging code to it.
The quickest way to get started is to download some sample code for your desired programming language and then search google for logging or plotting in that language (e.g. "how to log to csv in python") and add the code to the existing change handler.
Filtering
You can perform filtering on the raw data in order to reduce noise in your graph. For more information, see the Control Panel Graphing page.
Graph Type
You can perform a transform on the incoming data to get different graph types that may provide insights into your sensor data. For more information on how to use these graph types, see the Control Panel Graphing page.
We report the measured voltage in a ratiometric unit known as V/V. This is how the maximum range of sensors that use strain gauges is usually specified. V/V is the output value in V of the measured sensor, scaled for a 1V sensor supply voltage. This value will correspond to the physical quantity that the sensor is measuring, regardless of the actual voltage supplied to the sensor.
{
{{UGC-Entry|Connecting Your Strain Gauge or Load Cell| | Load cells are pressure sensors that can be used with the 1046. For more information, see our Load Cell Primer.
If no documentation is available for your strain gauge, it’s possible to use a multimeter to determine how to connect it, provided there are no electronics in the sensor. First, measure resistance between the 4 wires. There are 6 combinations - two combinations will have a resistance 20-40% higher than the other four. Choose one of these high-resistance combinations, and wire it into 5V and G on the 1046. Connect the other two wires into +/-. Apply a load, if the V/V responds in the opposite way to your expectations, flip the +/- wires.
The 1046 is designed to measure voltages as a ratio of the supply voltage - it’s not practical to make measurements of absolute voltages with this product.
For maximum accuracy, all wires from the 1046 to the sensor should be the same length and thickness. Changes in temperature will change the resistance of the wires - if they are all the same, the errors will cancel out.
Each bridge input can be powered down, reducing power consumption with 1046 sensors, and useful for reducing heating of sensors, which can introduce errors.
Load cells output a small voltage proportional to the amount of strain they are currently experiencing. The rated output for most load cells at full load is in the order of millivolts, so when you’re only straining the load cell at a fraction of its full load, you will get very small values. In order to convert to meaningful units like grams or newtons, you need to calibrate the load cell.
We have observed a 1.5% difference between a 1x gain and an 8x gain. This may require that each system (1046 and sensors) be calibrated as a whole. For maximum accuracy, decide on, and keep with a chosen gain before calibrating the system.
Expensive sensors will ship with a certificate of calibration specifying, often in mv/V, how the sensor responds to stimulus. Less expensive will have to be calibrated
For an in-depth guide on calibration, see Calibrating Analog Sensors.
Measuring Resistive Thermal Devices (RTD)
Using a Wheatstone Bridge
A Wheatstone bridge is the classic method of measuring unknown resistances, and requires three resistors of known values. It uses the current in each leg of the bridge to create a voltage differential between both voltage dividers. Using the voltage differential and the three known resistors, the resistance of the fourth resistor can be determined.
To determine the resistance of the RTD, the following formula can be used:
Where is the Bridge Value given by the PhidgetBridge (in mV/V) , and , and are the resistances of the known resistors.
Using a Voltage Divider
The alternate method requires only two resistors. This reduces the amount of error that can be introduced into the system due to resistor tolerances. A voltage is applied to the two resistors and the RTD in series. The voltage drop across the RTD is measured. Using the voltage drop and the values of the two resistors, the resistance of the RTD can be determined.
To determine the resistance of the RTD, the following formula can be used:
Where is the Bridge Value given by the PhidgetBridge (in mV/V) , and and are the resistances of the known resistors.
Getting Higher Accuracy
In order to get the highest accuracy from the RTD, consider the following:
- Use resistors with a high degree of tolerance. There will be less variability in the manufacturing of 0.1% resistors when compared to 1% resistors.
- Measure the known resistors with an ohmmeter. By obtaining the most accurate measurements for the known resistances, the formula will result in a more accurate measurement of the RTD.
- Use a moving average when obtaining the Bridge Value to reduce the amount of noise in the measured signal.
- Estimate or Measure the resistance of the +5V and GND wires between the RTD and the 1046 PhidgetBridge. Add this resistance to the two resistors.
- Turn off the power to the RTD (by disabling the channel on the PhidgetBridge) to reduce self-heating of the RTD.
- By using higher resistor values (> 1 Kilo ohm), there will be less self-heating of the RTD, but the resolution of the measurement will be reduced somewhat. We recommend 1 Kilo Ohm resistors as a reasonable trade off.
The Change Trigger is the minimum change in the sensor data needed to trigger a new data event.
The Data Interval is the time (in ms) between data events sent out from your Phidget.
The Data Rate is the reciprocal of Data Interval (measured in Hz), and setting it will set the reciprocal value for Data Interval and vice-versa.
You can modify one or both of these values to achieve different data outputs. You can learn more about these properties here.
Before you open a Phidget channel in your program, you can set these properties to specify which channel to open. You can find this information through the Control Panel.
1. Open the Control Panel and double-click on the red map pin icon:
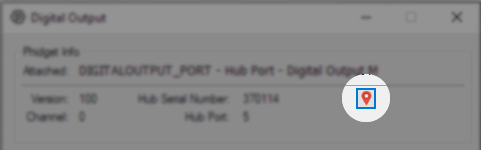
2. The Addressing Information window will open. Here you will find all the information you need to address your Phidget in your program.
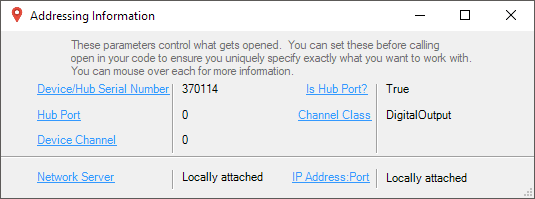
See the Phidget22 API for your language to determine exact syntax for each property.